Pottery Ball Mill
【Feeding size】:≤25mm
【Discharging size】:0.074-0.4mm
【Application】:The ball mill is used for grinding materials such as coal, pigments, and felspar for pottery. Grinding can be carried out either wet or dry but the former is carried at low speed.

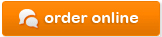
Pottery Ball Mill Description:
The pottery ball mill is usually used in the first segment of the two stages to discharge the rough ore. The pottery ball mill is roughly consist of the cylinder, cylinder liner,big gear ring, discharging pottery, and ore feeding device. There is a discharging pottery plate installed at the discharging end. In the head cover of the hollow shaft of the discharging end, it has bearing inner cover and discharging pottery installed and the later is made from central liner, pottery liner and dustpan liner etc. There are eight radial rib casted on the inner wall of the head cover, which divide the head cover into 8 fan rooms. Each room is installed dustpan liner, with the bolt fixed on the end cover. The pottery liner can be divided into two kinds of structure: one is formed by two pcs, pressed by the wedge block, which get fixed tightly on head cover with the bolt getting through the rib. The central part are supported by the central liner to prevent them from declining and dropping off. The other kind gets two pcs into one block, fixing with bolt directly. The central liner is star shape, formed by two block, tightened on the rib with the bolt.
The hole on the pottery liner depends on inclining direction. The width of the hole is gradually getting bigger to the discharging end, which can prevent the slurry from regorging and rough granularity from blocking. The slurry flow into the fan shape room through the hole on the pottery plate from the lower part of the discharging end, and get up to the upper part along the cylinder rotating and discharged off the hole path. The hollow shaft neck has the grinding proof inner cover, with one end made of trumpet shape blade to lead the slurry to flow out of the mill.
In this kind of mill the slurry is discharged through the pottery plate, it is called the pottery ball mill.
Pottery Ball Mill Characteristics and advantages
1. Fast discharging speed
2.high production capacity
3.High production capacity
4.Powers saving
5.Less overgrinding phenomena--discharging at the lower horizontal level
6.Less slurry stored inside -- easy to discharge the grinded fine particles in time
7.Much ball loading
Pottery Ball Mill Working principle:
The material spirally and evenly enters into the first warehouse of the ball mill along the input material hollow axis by input material device. In this warehouse, there is a ladder scale board or ripple scale board, and different specification steel balls are installed on the scale board. Cylinder rotation will generate centrifugal force and carries steel balls to a certain height. Then the steel balls falls strike and grind the materials. After being grinded coarsely in the first warehouse, the materials then enter into the second warehouse along the single insulation layer. In this warehouse, there is flat scale board with steel balls for further grinding. In the end, the power is discharged by output material board and the grinding operation is competed.
Model |
Cylinder rotary speed(r/min) |
Loading ball weight(t) |
Input size(mm) |
Discharge size(mm) |
Capacity(t/h) |
Motor power (kw) |
Weight (t) |
Ф900×1800 |
39 |
1.5 |
≤20 |
0.075-0.89 |
0.8-2 |
18.5 |
4.6 |
Ф900×3000 |
39 |
2.7 |
≤20 |
0.075-0.89 |
1-4 |
22 |
5.6 |
Ф1200×3000 |
36 |
3.5 |
≤25 |
0.074-0.4 |
1.6-5 |
37 |
12.8 |
Ф1200×4500 |
32 |
5 |
≤25 |
0.074-0.4 |
1.6-5.8 |
55 |
13.8 |
Ф1500×3000 |
27 |
7.5 |
≤25 |
0.074-0.4 |
2-5 |
75 |
15.6 |
Ф1500×5700 |
28 |
12 |
≤25 |
0.074-0.4 |
3.5-6 |
130 |
24.7 |
Ф1830×3000 |
25 |
11 |
≤25 |
0.074-0.4 |
4-10 |
130 |
28 |
Ф1830×6400 |
24 |
21 |
≤25 |
0.074-0.4 |
7-16 |
210 |
34 |
Ф1830×7000 |
24 |
23 |
≤25 |
0.074-0.4 |
8-18 |
245 |
36 |
Ф2100×3600 |
23 |
19 |
≤25 |
0.074-0.4 |
10-36 |
210 |
46 |
Ф2200×4500 |
21 |
27 |
≤25 |
0.074-0.4 |
12-23 |
280 |
48.5 |
Ф2200×6500 |
21 |
35 |
≤25 |
0.074-0.4 |
14-26 |
380 |
52.8 |
Ф2200×7000 |
21 |
35 |
≤25 |
0.074-0.4 |
15-28 |
380 |
54 |
Ф2200×7500 |
21 |
35 |
≤25 |
0.074-0.4 |
15-30 |
380 |
56 |
Ф2400×4500 |
21 |
30 |
≤25 |
0.074-0.4 |
18-45 |
320 |
65 |
Ф2400×8000 |
20 |
36 |
≤25 |
0.074-0.4 |
20-48 |
410 |
81 |
Ф2700×3600 |
21 |
39 |
≤25 |
0.074-0.4 |
19-75 |
400 |
83 |
Ф2700×4000 |
20 |
40 |
≤25 |
0.074-0.4 |
20-78 |
400 |
85 |
Ф2700×4500 |
20 |
48 |
≤25 |
0.074-0.4 |
22-85 |
430 |
89 |
Ф3200×4500 |
18 |
65 |
≤25 |
0.074-0.4 |
29-140 |
800 |
137 |
Ф3200×5400 |
18 |
81.6 |
≤25 |
0.074-0.4 |
30-180 |
800-1000 |
146 |
Ф3600×4500 |
17 |
88 |
≤25 |
0.074-0.4 |
35-210 |
1000 |
190 |
Ф3600×6000 |
17 |
117 |
≤25 |
0.074-0.4 |
38-240 |
1250-1500 |
220 |
Ф3600×8500 |
17 |
144 |
≤25 |
0.074-0.4 |
45-260 |
1800 |
260
|
You can fill out the form below and submit your contact information and product requirements to
us, we will contact you as soon as possible!
In order to get in touch with you in time, please be sure to complete your contact information
and requirements.